The Welding Process of ASTM A335 P11 Pipes 01
Project Overview
In an ethylene production capacity-expansion project of SINOPEC, thick-wall ASTM A335 P11 seamless pipes are required for the high-pressure steam pipeline distributed in several working zones. ASTM A335 P11 is a ferritic low alloy steel grade for high temperature service with deliberate addition of chromium and molybdenum. It has good creep strength at 450°C-550°C. However, there are some major challenges during its welding process including the hardening of heat-affected zone, cold cracks, PWHT, as well as hot cracks in service.
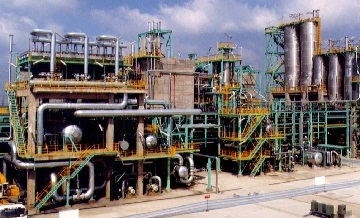
SINOPEC’s ethylene project in Wuhan, Hubei province.
The specification of ASTM A335 P11 seamless pipes covers(O.D x W.T): Φ323 mm x 45 mm, Φ356 mm x 47 mm, Φ406 mm x 54 mm, Φ508 mm x 66 mm and Φ609 mm x 78 mm. The elevation of the main pipeline structure is respectively old device zone[12.5 m], gasoline hydrogenation equipment [10.0 m], cracking zone [12.0 m], quenching zone [10.5 m], compressing zone [10.5 m and 9 m]. When the ethylene-production system starts, the high-pressure steam generated in the cracking furnace is transferred through the pipeline of ASTM A335 P11 seamless pipes to two turbines in old-device zone and other zones. Considering the severe service condition, 100% X-Ray inspection and 10% magnetic-particles inspection on each welding are required.
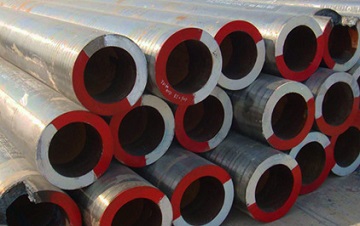
ASTM A335 P11 seamless pipes, 12″ x 45 mm, for the high-pressure steam line of an ethylene project.
Chemical Requirements and Properties
ASTM A335 P11 Chemical Composition % | ||||||
---|---|---|---|---|---|---|
C | Mn | P | S | Si | Cr | Mo |
0.05-0.15 | 0.30-0.60 | ≤0.025 | ≤0.025 | 0.50-1.00 | 1.00-1.50 | 0.44-0.65 |
*The carbon equivalent shall be calculated as per CE = C+Mn/6+(Cr+Mo+V)/5+(Si+Ni+Cu)/15 the result of which is 0.586%.
*The cold cracking susceptibility index Pcm = C+Si/30+(Mn+Cu+Cr)/20+Ni/60+Mo/15+V/10+5B is 0.24%.
Filler Metal Selection for ASTM A335 P11 Pipes
In light of “filler metal matching base metal” principle, welding wire ER80S-B2 and welding electrode E8018-B2 are selected. See the chemical composition and mechanical properties of the two filler metals listed below:
Chemical Composition of ER80S-B2, % | |||||||||
---|---|---|---|---|---|---|---|---|---|
C | Mn | Si | S | P | Ni | Cr | Mo | Cu | Sn |
0.09 | 0.52 | 0.49 | 0.008 | 0.008 | 0.04 | 1.04 | 0.50 | 0.004 | 0.004 |
Mechanical Properties of ER80S-B2 | |||
---|---|---|---|
Tensile Strength, [MPa] | Yield Strength, [MPa] | Elongation, [%[ | Impact Test @20°C Ave. [J] |
629 | 550 | 28 | 281 |
Chemical Composition of E8018-B2, % | ||||||||
---|---|---|---|---|---|---|---|---|
C | Mn | Si | S | P | Cr | Mo | Sn | Sb |
0.07 | 0.74 | 0.50 | 0.009 | 0.009 | 1.30 | 0.52 | 0.003 | 0.001 |
Mechanical Properties of E8018-B2 | |||
---|---|---|---|
Tensile Strength, [MPa] | Yield Strength, [MPa] | Elongation, [%[ | Impact Test @20°C Ave. [J] |
660 | 570 | 25 | 160 |
Typical Beveling End Design
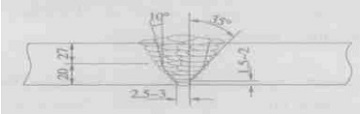
Typical beveling ends design for ASTM A335 P11 seamless pipes 356mm x 47mm, compound beveling acc. to ASME B16.25.
Preheating Before Welding
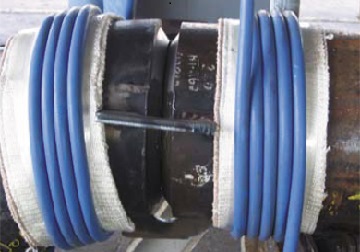
ASTM A335 P11 seamless pipes: preheating before welding.
The ASTM A335 P11 seamless pipes shall be preheated before welding by electromagnetic coils. Its preheating area and positioning are illustrated below. The preheating temperature shall be controlled between 200°C and 250°C and hold for at least 30 minutes before welding.
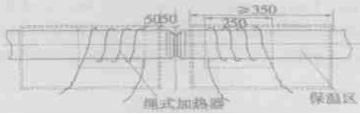
Coil-Preheating design before welding of A335 P11 seamless pipes.
Welding Process and Welding Parameters
Gas Tungsten Arc Welding(GTAW) is employed to produce the the preliminary welding seam between two ASTM A335 P11 pipes and manual arc welding(SMAW) should be conducted to fully cover the welding area. The flow rate of argon gas during welding is 10 L per minute. The interpass temperature shall be controlled between 200°C and 250°C. When the welding seam is higher than 15 mm or the welding is finished, a 300-350°C post-heating shall be implemented holding for at least 30 minutes. After welding area cools off, a post-welding heat treatment(PWHT) is conducted to relieve the stress by heating to 600-675°C and holding for 2.5 hours.