Incoloy 825 Quench Ring and Dip Tube for Gasifiers
Generally, a gasifier of Texaco coal gasification process consists of the upper combustion chamber and the lower cooling zone. The pressurized coal-water slurry is injected into the combustion chamber together with oxygen or air through a injection burner. A useful synthetic gas will be produced at a temperature of approx. 1400°C. Along with the hot gas, large amount of hot ash slags are generated. All the hot products shall be discharged to the cooling zone through a quench ring and dip tube structure. After been through the cooling zone, the temperature of the hot gas is reduced to about 300°C. And it is then directed to other facilities for further processing.
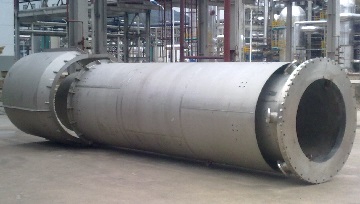
A quench ring fixed with the dip tube for Texaco coal-water slurry gasifier.
Both the quench ring and the dip tube are working in extremely harsh conditions: sudden temperature drop from 1400°C to 300°C; high pressures which may be as high as 25 MPa; severe corrosion and erosion caused by the hot gas & slag mixtures. Incoloy 825 is chosen for the fabrication of these components.
Function of The Incoloy 825 Quench Ring
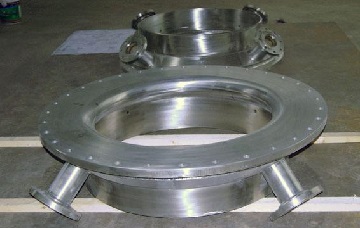
Incoloy 825 gasifier quench rings.
The main body of the Incoloy 825 quench ring is made of ASTM B424 UNS N08825 plates with cooling water inlet made of ASTM B564 UNS N08825 forgings. The quench ring can be furnished in either integral or segmented pattern. It is in close contact with the combustion chamber. The holding coolant in the quench ring flows down the internal surface of the adjacent dip tube and forms a film of water over the latter.
Function of The Incoloy 825 Dip Tube
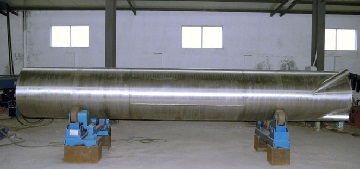
A dip tube made of Incoloy 825 plates manufactured to ASTM B704 Gr. N08825.
The dip tube is located below the quench ring. It is wetted by the coolant held by the quench ring. The lower serrated edge of the dip tube shall be dipped into the coolant. Hot gas and particulated slag will be passed through it and get cooled in the coolant. The dip tube shall be made from Incoloy 825 plates manufactured to ASTM B704 Gr. N08825.