ASTM A335 Seamless Ferritic Alloy Steel Pipe
ASTM A335 is the standard specification for seamless ferritic alloy steel pipe for high temperature service. It covers sever grades: P1, P2, P5, P5b, P5c, P9, P11, P12, P15, P21, P22, P23, P91, P92, P122, out of which P5, P9, P11, P22, P91, and P92 are most widely utilized in practice. The specification covers nominal wall and minimum wall chrome-molybdenum( also known as Cr-Mo, or Cr-Moly) alloy steel pipe intended for high-temperature application. Pipe ordered to this specification shall be suitable for bending, flanging(vanstoning), and similar forming operations, and for fusion welding. ASTM A335 P11, P22, P91 and P92 are commonly used in power plants and chemical-petrochemical industry, while P9 and P5 are mainly used in petroleum refineries. Hebei Metals supplies ASTM A335 Cr-Mo alloy steel seamless pipes sized from 1/2″ to 24″(NPS15 ~ NPS600) ranging in wall thickness from SCH20 to XXS or even thicker.
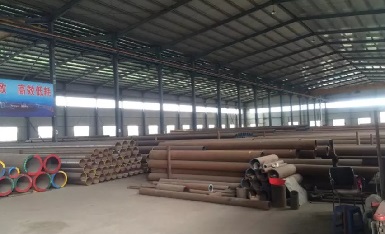
More than 32000 MT of all grades of ASTM A335 seamless pipes in stock including grades P11, P22, P91, P92 and P5, etc.
1. UNS Designations and Chemical Composition
ASTM A335/ A335M Chemical Composition % | |||||||||
---|---|---|---|---|---|---|---|---|---|
Grade | UNS | C | Mn | P | S | Si | Cr | Mo | Others |
P1 | K11522 | 0.10-0.20 | 0.30-0.80 | 0.025 | 0.025 | 0.10-0.50 | - | 0.44-0.65 | - |
P2 | K11547 | 0.10-0.20 | 0.30-0.61 | 0.025 | 0.025 | 0.10-0.30 | 0.50-0.81 | 0.44-0.65 | - |
P5 | K41545 | 0.15 | 0.30-0.60 | 0.025 | 0.025 | 0.50 | 4.00-6.00 | 0.45-0.65 | - |
P5b | K51545 | 0.15 | 0.30-0.60 | 0.025 | 0.025 | 1.00-2.00 | 4.00-6.00 | 0.45-0.65 | - |
P5c | K41245 | 0.12 | 0.30-0.60 | 0.025 | 0.025 | 0.50 | 4.00-6.00 | 0.45-0.65 | *A |
P9 | S50400 | 0.15 | 0.30-0.60 | 0.025 | 0.025 | 0.25-1.00 | 8.00-10.00 | 0.90-1.10 | - |
P11 | K11597 | 0.05-0.15 | 0.30-0.60 | 0.025 | 0.025 | 0.50-1.00 | 1.00-1.50 | 0.44-0.65 | - |
P12 | K11562 | 0.05-0.15 | 0.30-0.61 | 0025 | 0.025 | ≤0.50 | 0.80-1.25 | 0.44-0.65 | - |
P15 | K11578 | 0.05-0.15 | 0.30-0.60 | 0.025 | 0.025 | 1.15-1.65 | - | 0.44-0.65 | - |
P21 | K31545 | 0.05-0.15 | 0.30-0.60 | 0.025 | 0.025 | 0.50 | 2.65-3.35 | 0.80-1.06 | - |
P22 | K21590 | 0.05-0.15 | 0.30-0.60 | 0.025 | 0.025 | 0.50 | 1.90-2.60 | 0.87-1.13 | - |
P23 | K41650 | 0.04-0.10 | 0.10-0.60 | 0.030 | 0.010 | 0.50 | 1.90-2.60 | 0.05-0.30 | *B |
P36 | K21001 | 0.10-0.17 | 0.80-1.20 | 0.030 | 0.025 | 0.25-0.50 | 0.30 | 0.25-0.50 | *C |
P91 | K91560 | 0.08-0.12 | 0.30-0.60 | 0.020 | 0.010 | 0.20-0.50 | 8.00-9.50 | 0.85-1.05 | *D |
P92 | K92460 | 0.07-0.13 | 0.30-0.60 | 0.020 | 0.010 | 0.50 | 8.50-9.50 | 0.30-0.60 | *E |
P122 | K92930 | 0.07-0.14 | 0.70 | 0.020 | 0.010 | 0.50 | 10.00-11.50 | 0.25-0.60 | *F |
P911 | K91061 | 0.09-0.13 | 0.30-0.60 | 0.020 | 0.010 | 0.10-0.50 | 8.50-9.50 | 0.90-1.10 | *G |
*The UNS designation is established in accordance with Practice E527, and SAE J 1086 – Practice for numbering metals and alloys.
*All values are the maximum unless a range is furnished.
*A – 4 times of Carbon≤Titanium≤0.70% or Columbium:8 times of Carbon~10 times of Carbon.
*B – V:0.20-0.30, Cb:0.02-0.08, B: 0.0010-0.006, N:≤0.0015, Al:≤0.030, W:1.45-1.75, Ni:≤0.40, Ti: 0.005-0.060, Ti/N:≥3.5.
*C – Ni:1.00-1.30, Cu:0.50-0.80, Cb:0.015-0.045, V:≤0.02, N:≤0.02, Al:≤0.050.
*D – V:0.18-0.25, N:0.030-0.070, Ni:≤0.40, Al:≤0.02, Cb:0.06-0.10, Ti:≤0.01, Zr:≤0.01.
*E – V:0.15-0.25, N:0.03-0.07, Ni:≤0.40, Al:≤0.02, Cb:0.04-0.09, W:1.5-2.0, B:0.001-0.006, Ti:≤0.01, Zr:≤0.01.
*F – V:0.15-0.30, W:1.30-2.50, Cu:0.30-1.70, Cb:0.04-0.10, B:0.0005-0.005, N:0.040-0.1, Ni:≤0.5, Al:≤0.02, (Ti&Zr):≤0.01.
*G – V:0.18-0.25, Ni:≤0.40, Cb:0.060-0.10, B:0.0003-0.006, N:0.04-0.09, Al:≤0.02, W:0.90-1.10, Ti:≤0.01, Zr:≤0.01.
2. Mechanical Properties: Tensile, Yield, Elongation & Hardness
ASTM A335 Grade | Tensile Strength | Yield Strength | Elongation % | Hardness(HB) | |||
ksi | MPa | ksi | MPa | Longitudinal | Transverse | ||
P1 | 55 | 380 | 30 | 205 | 30 | 20 | - |
P2 | 55 | 380 | 30 | 205 | 30 | 20 | - |
P5 | 60 | 415 | 30 | 205 | 30 | 20 | - |
P5b | 60 | 415 | 30 | 205 | 30 | 20 | - |
P5c | 60 | 415 | 30 | 205 | 30 | 20 | - |
P9 | 60 | 415 | 30 | 205 | 30 | 20 | - |
P11 | 60 | 415 | 30 | 205 | 30 | 20 | - |
P12 | 60 | 415 | 32 | 220 | 30 | 20 | - |
P15 | 60 | 415 | 30 | 205 | 30 | 20 | - |
P21 | 60 | 415 | 30 | 205 | 30 | 20 | - |
P22 | 60 | 415 | 30 | 205 | 30 | 20 | - |
P23 | 74 | 510 | 58 | 400 | 20 | - | - |
P91 | 85 | 585 | 60 | 415 | 20 | - | ≤250 |
P92 | 90 | 620 | 64 | 440 | 20 | - | ≤250 |
P122 | 90 | 620 | 58 | 400 | 20 | - | ≤250 |
P911 | 90 | 620 | 64 | 400 | 20 | - | - |
*All values are minimum unless otherwise specified.
*The specimen for elongation test shall be in the gauge length of 2 inches or 50 mm(or 4D).
3. Heat Treatment and Delivery Conditions
ASTM A335 pipes may be either hot finished or cold drawn with finishing treatment listed below:
- Pipes of all grades of ASTM A335 except P5c, P23, P91, P92, P122, and P911 shall be reheated, and furnished in the full-annealed, isothermal annealed, or normalized and tempered condition, the minimum tempering temperature for grades P5, P5b, P9, P21, and P22 shall be 1250°F (675°C), the minimum tempering temperature for grades P1, P2, P11, P12, and P15 shall be 1200°F (650°C). It is recommended that the temperature for tempering should be at least 100°F (50°C) above the intended service temperature; consequently, the purchaser should advise the manufacturer if the service temperature is to be over 1100°F (600°C).
- ASTM A335 Pipe of Grades P1, P2, and P12, either hot finished or cold drawn, may be given a final heat treatment at 1200°F (650°C) to 1300°F (705°C) instead of heat treatments above-mentioned.
- Pipe of grade P5c shall be given a final heat treatment in the range from 1325°F (715°C) to 1375°F (745°C).
- ASTM A335 grades P92 & P911 shall be normalized at 1900°F (1040°C) minimum and tempered at 1350°F (730°C) minimum as a final heat treatment.
- Grade P122 shall be normalized at 1900°F (1040°C) minimum, and tempered at 1350°F (730°C) minimum as a final heat treatment.
- Grade P23 shall be normalized at 1900°F (1040°C) minimum with air cooling or accelerated cooling and tempered at 1350°F (730°C) minimum as a final heat treatment.
- ASTM A335 P91 shall be normalized at 1900°F (1040°C) minimum, and tempered at 1350°F (730°C) minimum as a final heat treatment. Alternatively, liquid quenching and tempering is allowed for thicknesses above 3 inch when mutually agreed upon between the manufacturer and the purchaser. In this case the pipe shall be quenched from 1900°F (1040°C) minimum and tempered at 1350°F (730°C) minimum as final heat treatment.
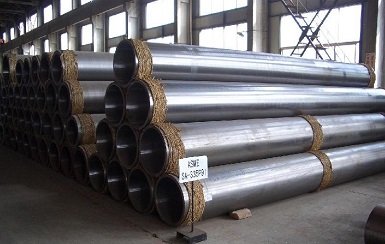
ASTM A335 P91 pipes, 12″ S40, for 300MW power plant steam pipeline.
4. Tests and Examinations
- Unless an alternative nondestructive electric test is selected or otherwise specified by the purchaser, hydrostatic test shall be performed for each length of ASTM A335 pipe.
- Mechanical Tests: pipes of all grades of ASTM A335 shall take transverse or longitudinal tension test and flattening test, hardness test, or bend test. The test will be made on 5% of the pipe from each heat number.
- The nondestructive test (NDT) shall be performed in accordance with Practice E 213, Practice E 309, or Practice E 570. These NDT methods includes: Ultrasonic Examination, which shall be performed to detect both longitudinally and transversely oriented discontinuities; Eddy Current Examination, which has the capability to detect significant discontinuities especially of short abrupt type; Flux Leakage Examination, which is capable of detecting the presence and location of significant longitudinally and transversely oriented discontinuities.
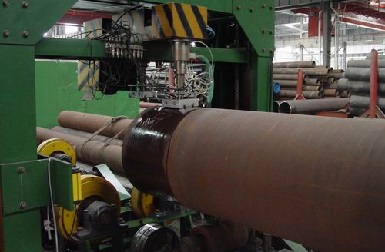
The Ultrasonic Test performed on an A335 P22 SMLS pipe, 16″ SCH80.
5. How to order an ASTM A335 Pipe
When asking for a quote, it will be very helpful if the client can provide detailed information:
- Name of material: seamless alloy steel pipe.
- Specific grades.
- Manufacture: hot rolled or cold drawn.
- Size: NPS+Schedule Number; O.D+Nominal W.T; O.D+Minimum W.T; I.D+ Nominal W.T; I.D+Minimum W.T.
- Length(fixed or random) and Quantity.
- End Finish(butt welding ends or plain ends).
An example: ASTM A335 Gr. P11 SMLS Pipe, 12″ SCH80, Length=6 m, cold drawn, BW ends, 225 pieces.
6. Equivalent Alternatives
The alternative to certain grade of ASTM A335 can be found in ASTM A426 and ASTM A369. ASTM A426 is the standard specification for centrifugally cast ferritic alloy steel pipe for high-temperature service. ASTM A369 is the standard specification for carbon and ferritic alloy steel forged or bored pipe for high-temperature service. Both of them specify relatively equivalent grades of Cr-Mo alloy steel pipe. The main difference between ASTM A335, ASTM A426, and ASTM A369 is the manufacture of the pipe: ASTM A335 – hot rolled or cold drawn; ASTM A426 – centrifugal casting; ASTM A369: forging.
Other standards related to the seamless Cr-Mo alloy steel pipe include: ASTM A213 – standard specification for seamless ferritic and austenitic alloy steel boiler, superheater, and heat exchanger tubes; ASTM A199 – standard specification for seamless cold drawn intermediate alloy steel heat exchanger and condenser tubes; ASTM A200 – standard specification for seamless intermediate alloy steel tubes for refinery service.