ASTM A335 P92
1. The Development of ASTM A335 P92
In order to improve the heat efficiency of reheating steam pipeline in power plant, the reheating-temperature can be designed as high as 621°C, which is known as the super-critical temperature. The Unite States firstly developed ASTM A335 P92 alloy steel in late 1980’s to meet the heat-resisting requirements of such a high-temperature power unit. The alloy steel P92 is an improved version of ASTM A335 P91 alloy which has deliberate addition of tungsten, vanadium, niobium, decreased amount of molybdenum to fine-tune to ferrite/austenite ratio, as well as carefully controlled amount of boron and nitrogen.
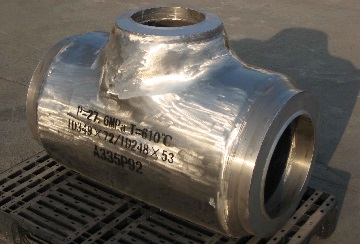
A reducing tee of ASTM A335 P92 for power plant steam line, runlet:(I.D)349×72 mm, outlet:(I.D)248×53 mm, design temperature: 610°C, design pressure: 27.6MPa.
Designated as UNS K92460, ASTM A335 P92 is also known as 9Cr-2W alloy steel. Its equivalent includes ASTM A213 T92, ASME SA335 P92, ASME SA213 T92, as well as EN standard X10CrWMoVNb9-2. The Grade P92 are generally furnished as seamless pipes, tubes, or fittings.
2. Chemical Requirements of ASTM A335 P92
Element | Carbon | Manganese | Phosphorus | Sulfur | Silicon | Chromium | Molybdenum | Others |
---|---|---|---|---|---|---|---|---|
Content, % | 0.07-0.13 | 0.30–0.60 | ≤0.020 | ≤0.010 | ≤0.50 | 8.50-9.50 | 0.30-0.60 | * |
3. Mechanical Properties of ASTM A335 P92
Tensile Strength, min. | Yield Strength, min. | Elongation %, min. | |||
---|---|---|---|---|---|
ksi | MPa | ksi | MPa | Longitudinal | Transverse |
90 | 620 | 64 | 440 | - | 20 |
4. Heat Treatment
![ASTM A335 P92 seamless pipes, 406 mm x 72 mm[w.t].](http://www.metalspiping.com/wp-content/uploads/2017/01/406x72mm-astm-a335-p92-seamless-pipes.jpg)
ASTM A335 P92 seamless pipes, 406 mm x 72 mm[w.t].
The Grade P92 of ASTM A335 shall be normalized at 1900°F [1040°C] minimum and tempered at 1350°F [730°C] minimum as a final heat treatment. After heat treatment, the hardness shall not exceed 250 HB/ 265 HV [25 HRC].